Importers continue to struggle as the supply chain’s woes continue. While down from their peaks earlier in the year, ports are still dealing with ships stuck at anchor and overcrowded container yards that they’re unable to clear.
And disruptions are set to grow, as freight’s “peak season” begins this month with the influx of goods for the back-to-school and holiday seasons.
Peak Season: Shipping’s peak season typically begins in late June, but importers got a bit of a jump on it this year. Imports at major U.S. ports were up 6.6% in the first quarter year-over-year, according to Beacon Economics, a research and consulting firm, and that added container volume is expected to further snarl congested ports.
- Gene Seroka, executive director of the Port of Los Angeles, told the Wall Street Journal, “They will continue to be tight until early next year if we don’t increase the velocity of getting them off the ships and off the port.”
Historically, getting goods from a factory in China to their recipient in the U.S. has taken about 45 days. Supply chain congestion has grown that timeline to more than 100 days, shippers say.
The Promo Perspective: Shipping and “peak season” has been as chaotic for promo importers as it has for other industries, but they are managing the disruptions. Trevor Gnesin, CEO of Tustin, California-based Logomark, says, “This is traditionally the case every year, so we are used to it, but yes, with the situation that we have at this time, it does put additional pressure to the supply chain.”
Bill Barrett, senior vice president of programs at Sterling, Illinois-headquartered HALO, says, “The supply chain disruptions that have impacted all industries over the past few years have diluted the ‘traditional’ peak shipping seasons. Delays due to manufacturing challenges, lockdowns or port congestion have delayed shipments and compressed shipping schedules so that the seasonal peaks seem to be one consistent flow of goods.
“We work with our account executives, supplier partners and manufacturers to accelerate our production timelines whenever possible so that we can account for any unforeseen challenges and deliver to our clients on time.”
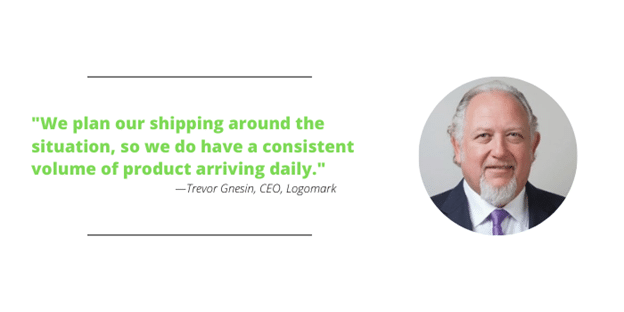
Gnesin says, “We plan our shipping around the situation, so we do have a consistent volume of product arriving daily.”
Part of equation is keeping customers informed on how shipping challenges affect their timelines. Barrett says, “Our global sourcing, import compliance and logistics teams maintain contact with our account executives during the importing process so that they can keep their clients updated and manage commitments.”
The Port Situation: Conditions at ports have improved in several different ways. The number of ships waiting outside the ports of Los Angeles and Long Beach has dropped from a peak of more than 100 vessels at the beginning of the year to approximately 30 ships today. The cost of shipping a container to the U.S. has dropped considerably. Freight rates are averaging around $8,000 per container this year, less than half of what shippers were paying late in 2021.
But challenges remain:
- Warehouses are full and trucking companies and railroads don’t have the equipment or workers they need.
- About 40% of the containers that arrive at the Port of Los Angeles are moved out via rail, but only about half of those coming in each day are loaded onto trains.
- Making matters worse, rail companies let a lot of their workers go during the pandemic and are having trouble restaffing as many have since taken better-paying jobs.